Table of Contents
How I recommend exact model for crushed bentonite clay?
Lnear vibratory screener, probability vibrating screen, gyratory screener, rotary vibro sieving machine, all of these sieving machines can process the bentonite, which one is the better one? I will explain the choosing.
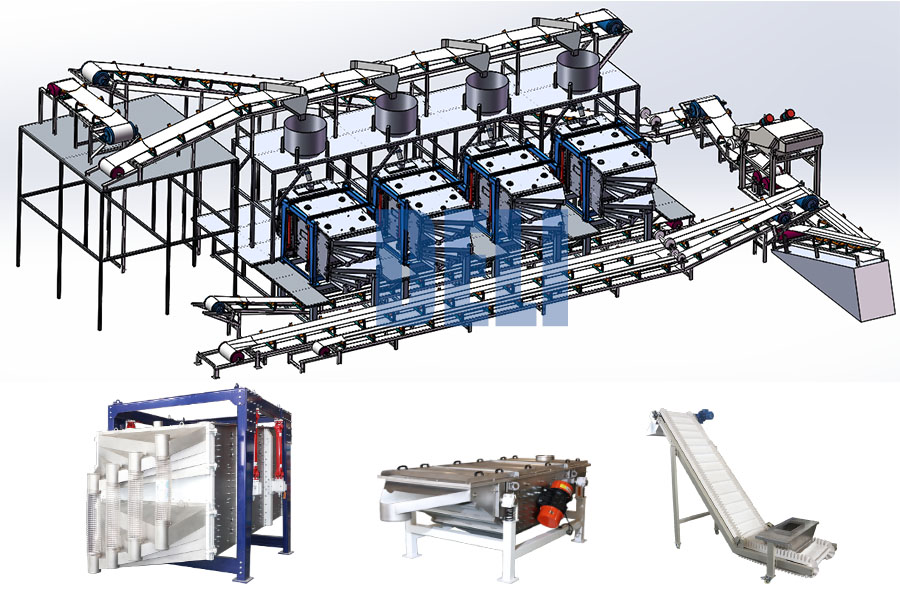
Clarify the purpose of screening
The customer’s final product is 0.1mm~1mm bentonite granule and 1mm~6mm bentonite particles. Customers tend to use 5-layer screens, which can improve screening efficiency, and some customers‘ clients require bentonite particles with a particle size of 2mm~6mm.

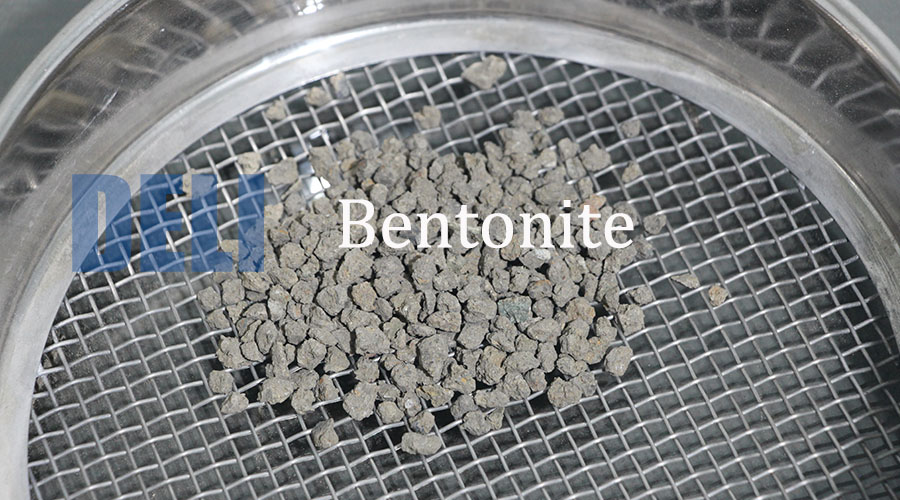
requirement data
Through the following table, this needs to be obtained through communication with the customer, we get some necessary data, which can help me accurately understand the customer’s sepration needs.
- The product is dry bentonite clay, which moisture is less than 5%.
- The sieving output is 10 tons per hour.
- The equipment that transports products to the screening machine is an automatic belt conveyor.
- 5-layer screen can obtain 6 kinds of finished products with different particle sizes at the same time.
- Mesh size is 0.1mm, 0.5mm, 1mm, 2mm, 6mm.
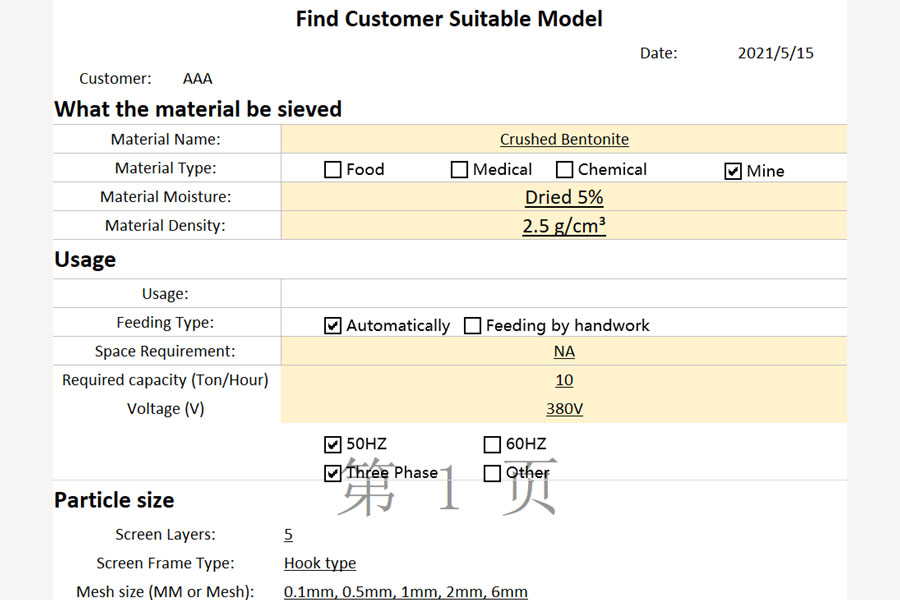
Screening machine recommendation
The conclusion is that I recommend the rectangle gyratory screener. First of all, because the minimum mesh required is 0.1mm, which is very fine, we can see in the table below that only rotary vibrating screen, circular tumbler sieving machine, rectangle swing screening machine, and air flow sifter can meet this requirement. Secondly, the screening output required by the customer is 10 tons per hour. Obviously, the only option is gyratory screener.
The customer didn’t ask me why I didn’t choose a linear vibrating screen, because the customer had already used a linear sieve machine and it performed poorly. The mesh was often blocked and the screening quality was very low.
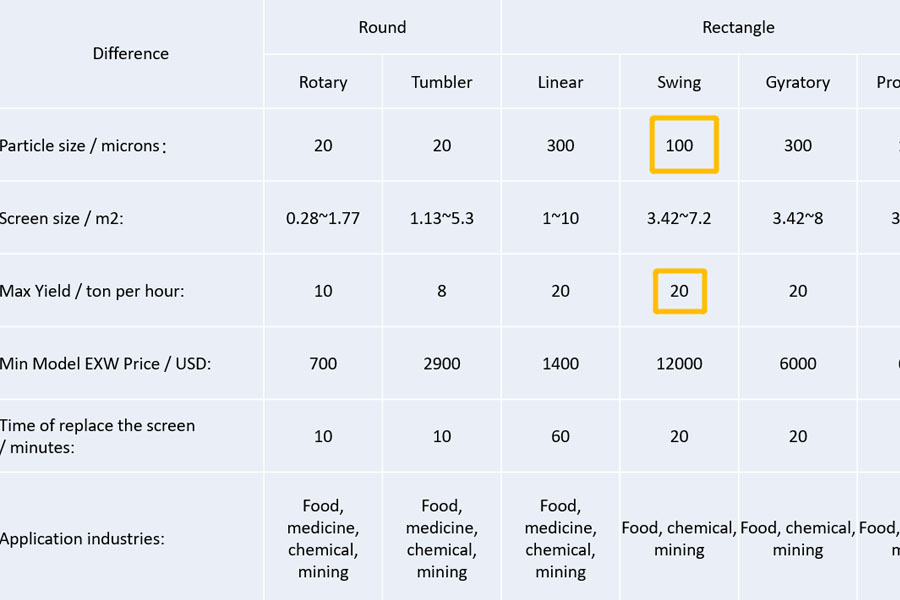