
Table of Contents
vibration sieve machine position in the manufacturing process of quartz powder
Quartz powder is widely used in glass, ceramics, artificial marble, foundry sand, high-purity metal silicon, metallurgy and other industries. The processing flow of quartz powder is crushing, washing, drying, iron removal, grinding and grading. The screen separator is located after drying and before packaging in the production process.
Screening machine effects the quality of quartz powder
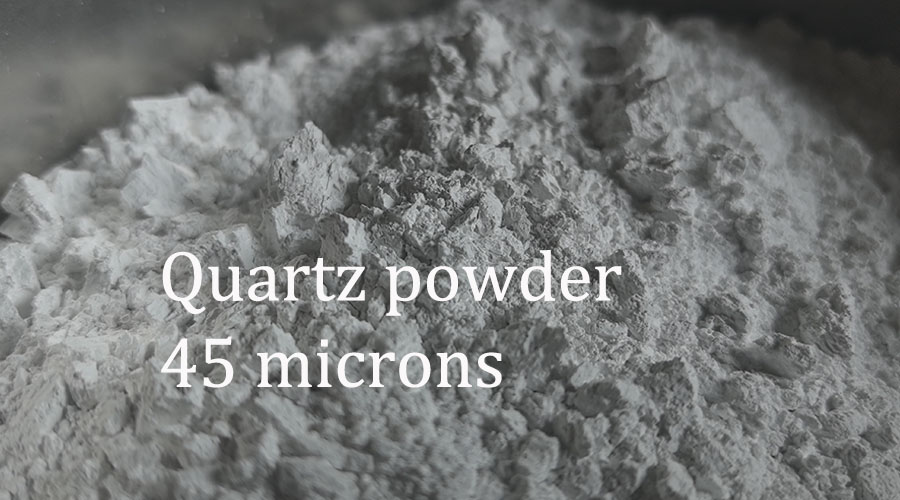
Quartz powder has a variety of specifications and indicators. The better the indicators, the higher the quality of the quartz powder and the stronger the competitiveness of the product. Among these indicators, three physical indicators are closely related to the vibration screen: particle size, hardness and iron content.
Quartz powder particle size
The particle size range of quartz powder is 200-800 mesh, and the common particle size specifications are 200 mesh, 325 mesh, 600 mesh, 800 mesh, and 1500 mesh. DELI’s tumbler sieve machine can screen quartz powder above 325 mesh.
What is the concept of 325 mesh (45 microns)? It is smaller than the flour in our lives. Flour is only 80 mesh (180 microns). Quartz powder is an ultra-fine powder. Visit more information of the mesh size.
The difficulty faced by ultra-fine powder separating is the problem of hole blocking. The figure below is a 325-mesh wire net screen. It looks like a mirror. It is difficult to see the existence of the mesh with the naked eye. The powder can easily block the mesh. DELI’s ultrasonic tumbler screening machine uses an ultrasonic screen cleaning system, which transmits ultrasonic waves to the screen. Each steel wire of the screen generates an overclocked vibration of 36GHZ, which then assists the quartz powder to pass through the mesh to achieve the purpose of screening.
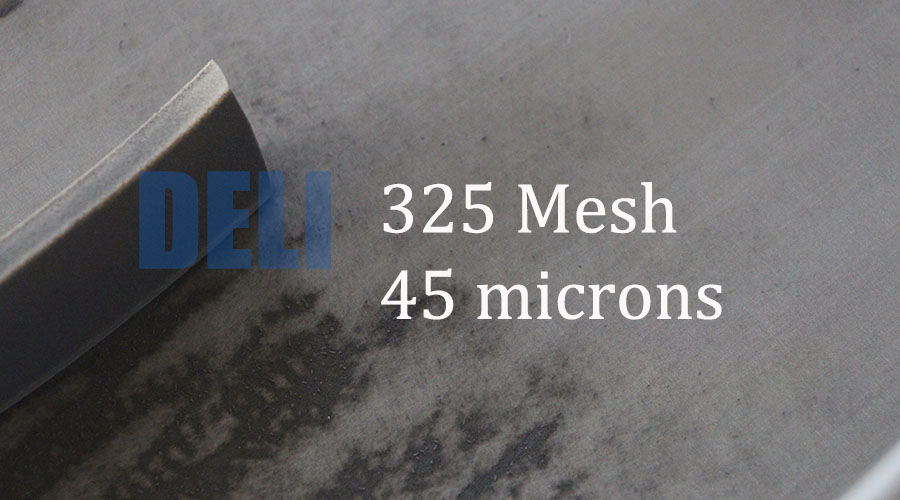
Quartz powder hardness effects vibrating screen working time.
Quartz powder has a high hardness, with a Mohs hardness of 7, and requires high wear resistance for industrial vibrating screens. The parts of the vibrating screen equipment that come into contact with quartz powder during the screening process are the woven screen, bottom spacer and discharge port. How to prevent quartz powder from wearing and corroding the parts of the vibrating screen after long-term use? First of all, we need to use thicker stainless steel plates in key parts, such as 3mm thickness, to solve the problem of wear of spacers and discharge ports. Secondly, DELI’s vibrating screen uses a screen with a tension of up to 20N meters, which will greatly extend the life of the woven screen.
Mesh NO. | Mesh size MM | Screen tension |
100M | 150 Microns | 17N |
200M | 75 Microns | 18N |
325M | 45 Microns | 20N |
Avoiding extra iron come into quartz powder during sieving
Quartz powder has very high requirements for iron content, especially in the marble tile and glass industries, as iron can cause the color of tiles to change.
We use physical iron removal methods and install a set of iron removers at the outlet of the vibrating screen. We use the principle of magnets absorbing iron impurities to remove iron from quartz powder.